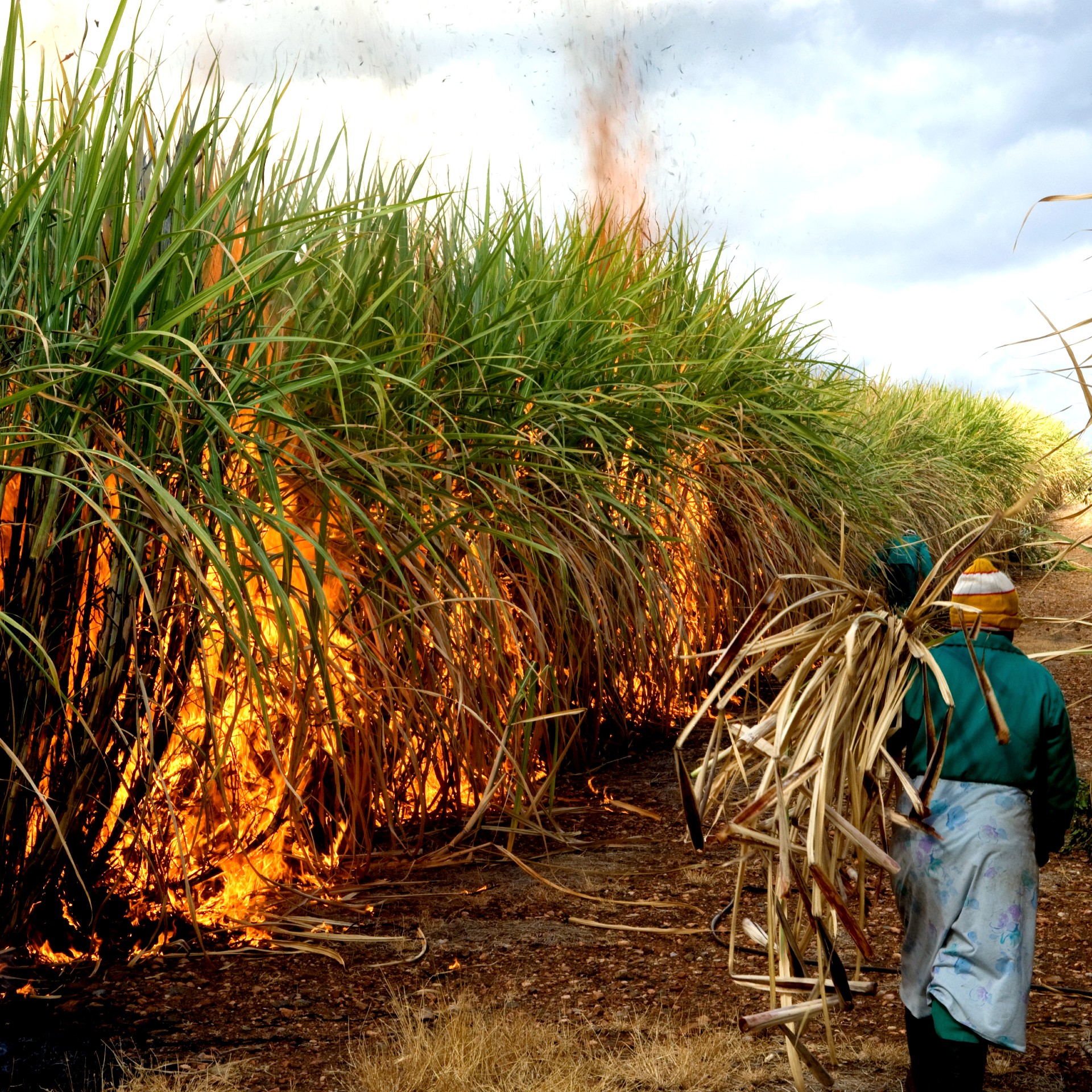
Many people are surprised to learn that sugar is used in ethanol. Ethanol is a fuel that is made by blending a variety of substances. For example, corn and a small amount of water are combined to make ethanol. In addition, it contains a range of other materials that contribute to its taste and safety. These include Yeast and Lignocellulose.
Yeast
The most common microorganisms used in ethanol production are yeasts. They break down the sugars from plants into ethanol fuel. A large variety of yeasts is used in the fermentation process; some are better at fermenting than others.
Several yeast species will only produce ethanol in an anaerobic environment. Some strains may even oxidize pyruvate to carbon dioxide. In addition to converting simple sugars into alcohol, yeasts can also be used to produce wine, a fermented beverage made from grape juice.
In recent years, increased interest has been shown in the use of yeast for bioethanol production. Bioethanol can be produced from various feedstocks, including corn, forestry byproducts, and perennial grasses. This article explores the characteristics that make specific yeasts more suitable for ethanol production and the environmental conditions associated with wine production.
Saccharomyces cerevisiae is a highly productive fungus for ethanol. But its genetic components still need to be better understood.
Lignocellulose
Lignocellulose is used in ethanol production as a fuel. It provides an ideal alternative for fuels that can be used without polluting the environment. However, producing lignocellulosic ethanol at scale takes work. Several factors affect the cost and environmental performance of a bioethanol plant.
A large amount of research has been conducted on the conversion of various types of biomass to fuels. For instance, agricultural wastes, woody wastes, and glycerol from the biodiesel industry are studied. This research has revealed that biomass is one of the only renewable energy sources that can be utilized to produce fuels.
Lignocellulosic cellulose is cheaper than other biomass sources and has a higher net energy output. Therefore, lignocellulosic bioethanol can be produced from a wide range of renewable resources.
Enzymatic hydrolysis, distillation, and product/coproduct recovery are the main processes for producing bioethanol. The ethanol yield is affected by the type of feedstock.
To make bioethanol more economically viable, it is essential to optimize the entire process. Biorefineries are one of the solutions. These integrated plants offer opportunities for the whole of the production chain. They have the potential to solve many current environmental issues.
Increasing the blend rate above 10% ethanol could consume more corn.
In the last decade, the federal government put in place several mandates to encourage the production of biofuels. The most recent is the Renewable Fuel Standard (RFS). Specifically, the RFS requires the use of corn-based ethanol in transportation fuels.
Ethanol is a fuel that can be blended into gasoline to reduce vehicle emissions and improve air quality. It also helps lower consumer fuel prices.
Aside from its prominent contribution to clean air, ethanol can also help America become more energy-independent. It provides an alternative to the additives used in gasoline and helps cut carbon emissions from our cars. However, increasing the amount of ethanol in our vehicles could result in the consumption of more corn.
Unlike petroleum-based gasoline, ethanol produces more energy than it consumes. This is because it contains more oxygen than gasoline. Additionally, the octane number of ethanol is higher than gasoline, resulting in better engine performance.
While the ethanol industry claims that a higher blend of ethanol will improve fuel efficiency in modern engines, this claim needs to be more truthful. Two factors determine a blend’s impact on fuel economy. These factors include the blend’s ethanol content and its engine design.
Bioplastics made from sugarcane
Sugar cane is a fast-growing, water-loving plant that can be grown on degraded pasture land. The leaves of the plant absorb carbon dioxide and release it during photosynthesis. For every 1 kg of sugar cane, about 2.1 to 2.5 kg of CO2 is removed from the atmosphere.
However, large plantations often use herbicides, fertilizers, and other chemicals that can harm the environment. Using a chemical process to convert ethanol into plastic is one way to reduce the adverse effects.
The resulting plastics are made from renewable materials and have a positive carbon footprint. Several certification bodies provide labels indicating the proportion of renewable raw materials in a product.
Currently, most plastics are made from fossil fuels. While these products are considered sustainable, the carbon footprint is high. Many plastics are contaminated with toxic chemicals.
Bioplastics made from sugarcane have the potential to become a sustainable alternative to petroleum-based plastics. But the technology is new and still in development.